Discover What is Porosity in Welding and Its Result on Structural Stability
Discover What is Porosity in Welding and Its Result on Structural Stability
Blog Article
Recognizing Porosity in Welding: Exploring Reasons, Effects, and Avoidance Methods
Porosity in welding is a persistent challenge that can significantly affect the high quality and honesty of welds. As experts in the welding sector are aware, understanding the causes, results, and prevention methods associated with porosity is vital for attaining durable and reliable welds. By delving right into the source of porosity, examining its destructive impacts on weld quality, and discovering effective prevention techniques, welders can boost their expertise and skills to generate top quality welds constantly. The elaborate interaction of factors contributing to porosity needs a thorough understanding and a proactive strategy to make sure effective welding outcomes.
Common Sources Of Porosity
Contamination, in the kind of dirt, oil, or rust on the welding surface, develops gas pockets when warmed, leading to porosity in the weld. Improper protecting happens when the securing gas, commonly utilized in processes like MIG and TIG welding, is not able to fully safeguard the molten weld swimming pool from responding with the bordering air, resulting in gas entrapment and succeeding porosity. Furthermore, poor gas coverage, usually due to wrong circulation rates or nozzle positioning, can leave parts of the weld unsafe, allowing porosity to create.
Effects on Weld Top Quality
The visibility of porosity in a weld can significantly jeopardize the total high quality and integrity of the welded joint. Porosity within a weld produces voids or tooth cavities that weaken the structure, making it extra vulnerable to cracking, rust, and mechanical failure.
Moreover, porosity can prevent the efficiency of non-destructive screening (NDT) methods, making it testing to identify various other problems or interruptions within the weld. This can bring about considerable safety issues, particularly in important applications where the structural stability of the welded elements is paramount.
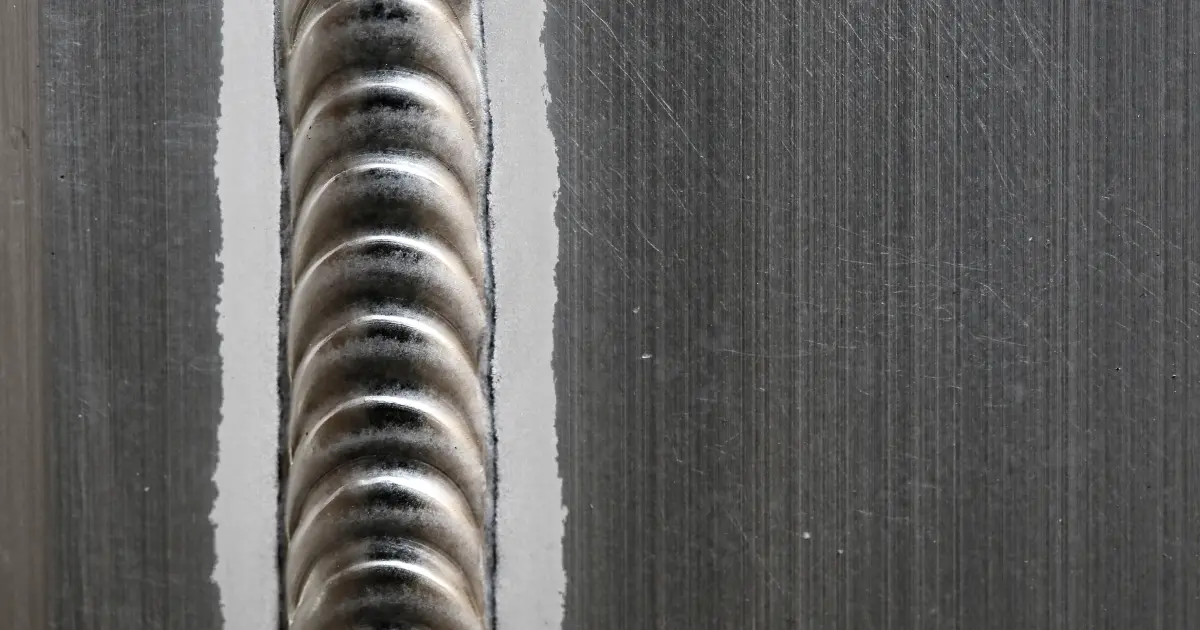
Avoidance Techniques Overview
Offered the damaging influence of porosity on weld quality, efficient avoidance strategies are essential to preserving the architectural stability of welded joints. Furthermore, selecting the ideal welding specifications, such as voltage, current, and take a trip speed, can assist minimize the go to this website threat of porosity development. By including these prevention methods into welding methods, the occurrence of porosity can be considerably reduced, leading to stronger and a lot more reputable bonded joints.
Relevance of Appropriate Protecting
Appropriate shielding in welding plays a vital function in preventing climatic contamination and making certain the honesty of bonded joints. Securing gases, such as argon, helium, or a mix of both, are typically made use of to protect the weld pool from reacting with elements airborne like oxygen and nitrogen. When these responsive elements enter into call with the warm weld swimming pool, they can cause porosity, resulting in weak welds with decreased mechanical properties.
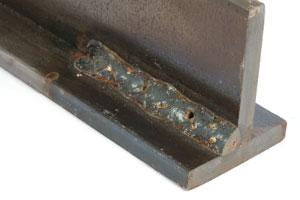
Insufficient protecting can lead to different problems like porosity, spatter, and oxidation, jeopardizing the structural integrity of the welded joint. Adhering to appropriate protecting techniques is vital to create top quality welds with minimal flaws and make sure the longevity and integrity of the bonded parts.
Surveillance and Control Approaches
Exactly how can welders properly keep track of and control the welding procedure to guarantee ideal results and avoid issues like porosity? By constantly keeping track of these variables, welders can identify inconsistencies from the ideal problems and make prompt adjustments to avoid porosity development.

In addition, executing appropriate training programs for welders is essential for checking and managing the welding process effectively. What is Porosity. Educating welders on the significance of keeping constant parameters, such as appropriate gas securing and travel speed, can assist stop porosity issues. Regular analyses and accreditations can likewise make sure that welders excel in monitoring and regulating these details welding procedures
Furthermore, making use of automated welding systems can improve tracking and control abilities. These systems can precisely control welding specifications, lowering the chance of human error and guaranteeing consistent weld high quality. By combining innovative monitoring technologies, training programs, and automated systems, welders can efficiently keep track of and control the welding procedure to reduce porosity issues and accomplish high-quality welds.
Verdict

Report this page